 |
Liquid Painting Plants |
 |
Liquid painting is used to give high quality asthetic finishes and can be applied on – metal, plastic and wood. High quality, multilayered paints can be applied in these virtually dust free Crescent plant designs.
There are various Liquid Painting processes meant for different substrates, shape of components based on ultimate Finish and Quality requirements.
The following can be the general classification:
- Multi Layers (Coats) Liquid Painting Lines :
The most common liquid painting line uses Wet-on Wet or Bake-on-Bake – 2 or 3 coats of paints one over the other. A typical line may be Primer coat followed by Top/Metallic coat and further followed by Clear/Lacquer coat. This is done after adequate surface preparation.
The paint application system may be HVLP, Electrostatic, Airless, Bells or Discs depending on the shape of the components, production volumes , paint consumption and the type of paint. The application process can be automated like Auto Guns on Reciprocators or Painting Robots .
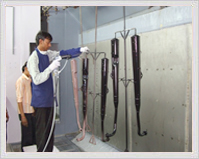 |
 |
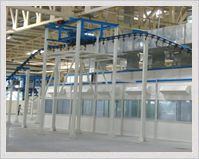 |
Two coat painting process for mufflers painting |
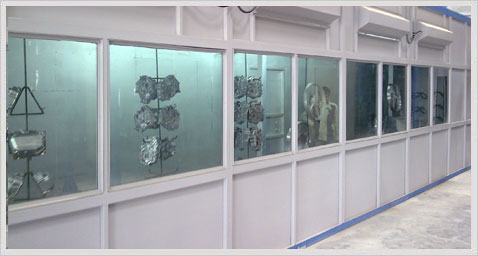
Liquid Painting Plant for Aluminum die casted component and alloy wheels.
-
Liquid ainting on Large components/machinery :
Large components like parts of earth moving or big machines are shot-blasted, followed by primer and top coats of paint. The primer coat is followed by top coat which is normally PU paint and is force dried in the oven at 70-800 C.
These pants can be supplied with separate booths and curing ovens with material movement for large sized components or a combined Spray booth cum curing oven may be provided.
- Plastic Coating Lines :
Several automotive parts like bumpers, mirror housing, car light housings, etc. are painted in different colors to match the shade of the original vehicle. Also cell phones, laptops, computer peripherals etc., are very popular to use special coating technology on plastic parts. There are different types of plastics and the choice of the painting process depends on end use requirements and the type of plastics.
A typical Plastic Painting line is Manual wiping with a suitable chemical (I/P) or spray pre-treatment, De-ionising process to remove the electrical charges on the parts, flaming with gas flame to increase the surface energy to facilitate paint adhesion.
The painting process includes conductive primer, flash-off, base coat, flash-off, clear coat, flash-off, oven for paint drying, cooling etc. The most important aspect of the Plastic Painting process is to maintain temperature and humidity level within the tolerance limit acceptable to the paint being used. Dust level control is another most important aspect for Plastic Painting Lines.
- Wood Coating Lines :
typical wood coating lines use ground conveyor system, dust free paint booths for paint
application followed by forced drying ovens in dust controlled environment. A combination of Dust free Spray booth cum
Curing oven may also be provided for wood Painting.
- Shower Coating :
Large size radiators, fuel tanks and transformers with fins having longer depth will prevent the paint spray from entering between the fins. For this application, the shower coating with good paint circulation system followed by paint curing in an oven is an ideal process.
|
|
 |
|
|
|